At MAKAI Power Catamarans, we take no shortcuts and use premium materials throughout the construction process. No shortcuts means carefully laying the best materials for the job, and then conducting a vacuum resin infusion process.
Our goal at MAKAI is to build the best boat, and for us that means the strongest result, and a finish you could eat off. This is the culmination of revolutionary design, thorough engineering, and cutting edge technology, executed with boatbuilding craftsmanship.
Following previous posts on choosing the best propulsion and best engines for your MAKAI, here we have a closer look at our vacuum infusion process and a description of the materials used.
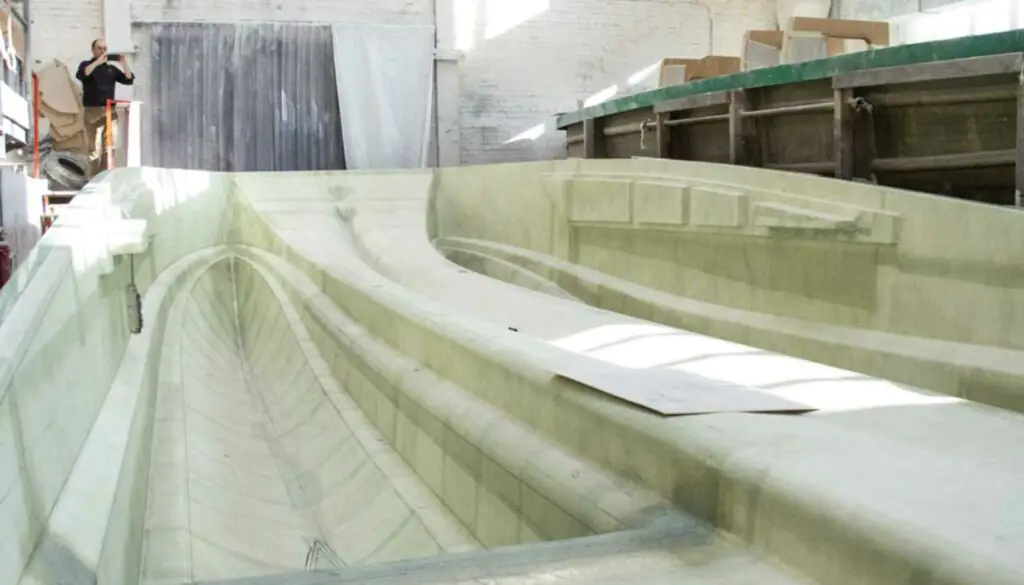
CORE MATERIALS
Our hulls are foam cored to achieve light weight, with maximum strength. The foam used is Divinycell, and the glass used is a combination of triaxial and quadraxial – in summary, the most expensive materials on the market today…
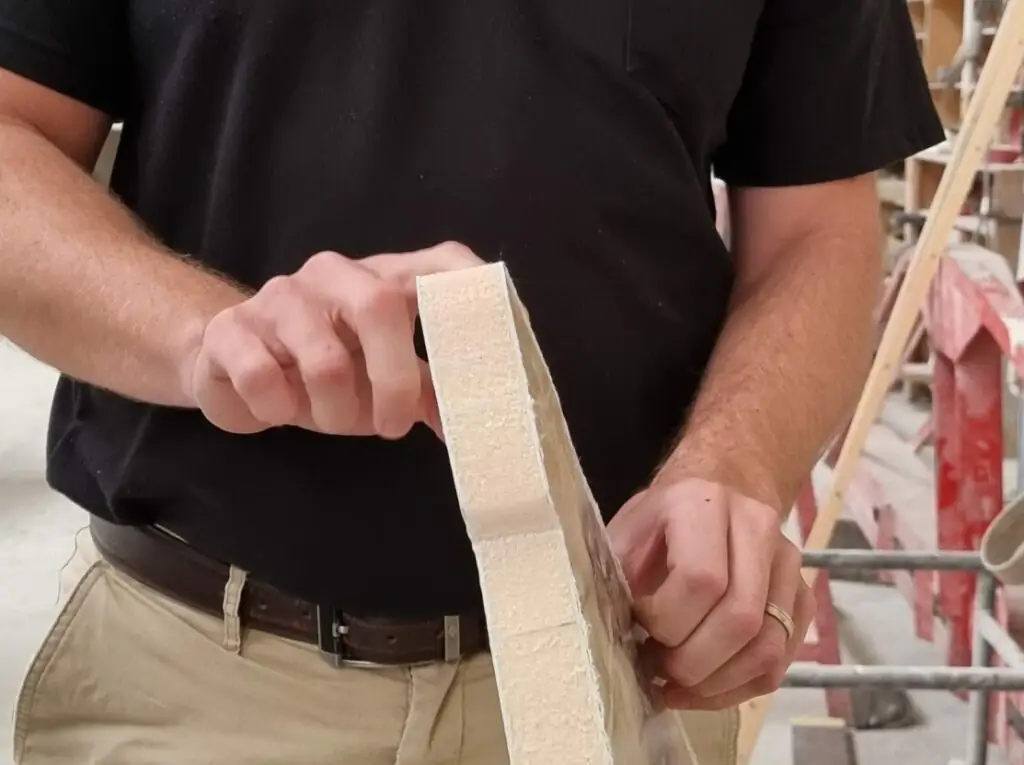
VACUUM INFUSION
Vacuum infusion allows for thorough soak-through of resin throughout the materials, while ensuring the lowest possible weight by removing any excess. Careful calculation is also required – the exact correct amount of resin should be consumed in the boat. And for us, that’s exactly what happened.
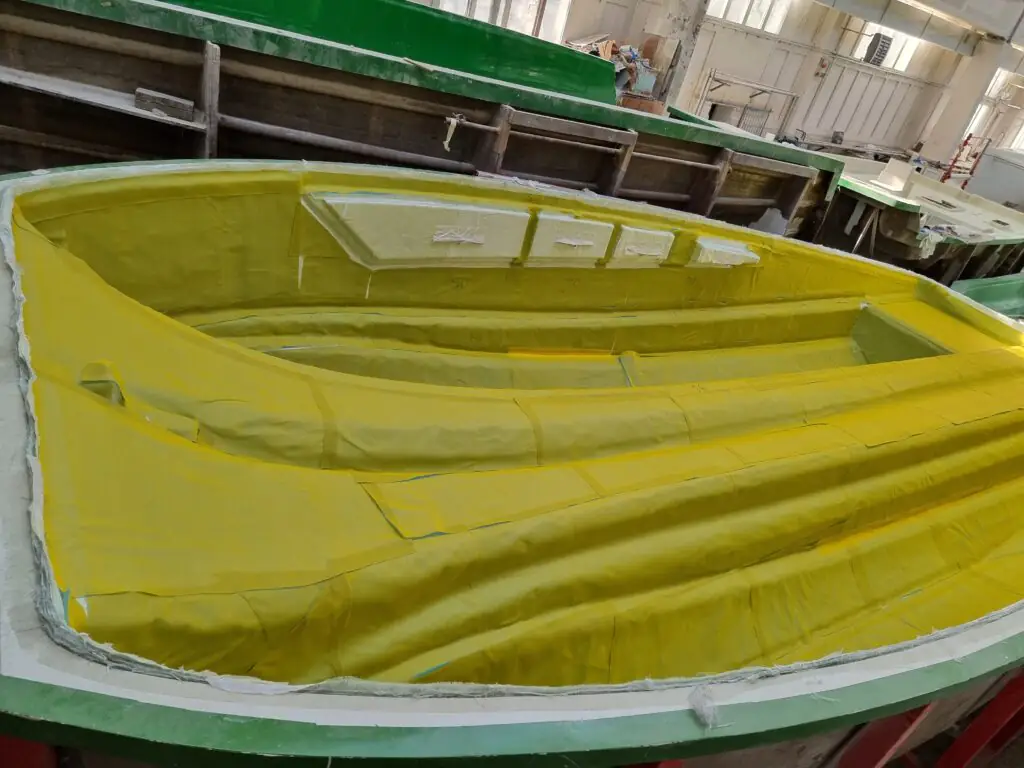
Once every layer is properly stacked and placed and covered with flow-mat the hull will then be covered with a single strong air-tight plastic cover.
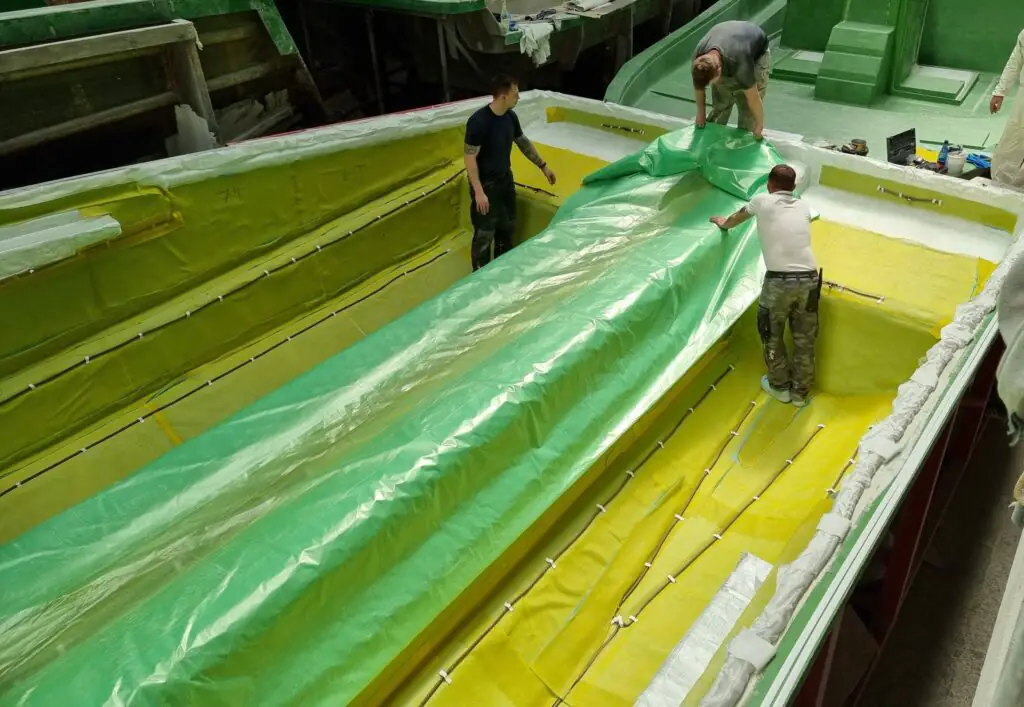
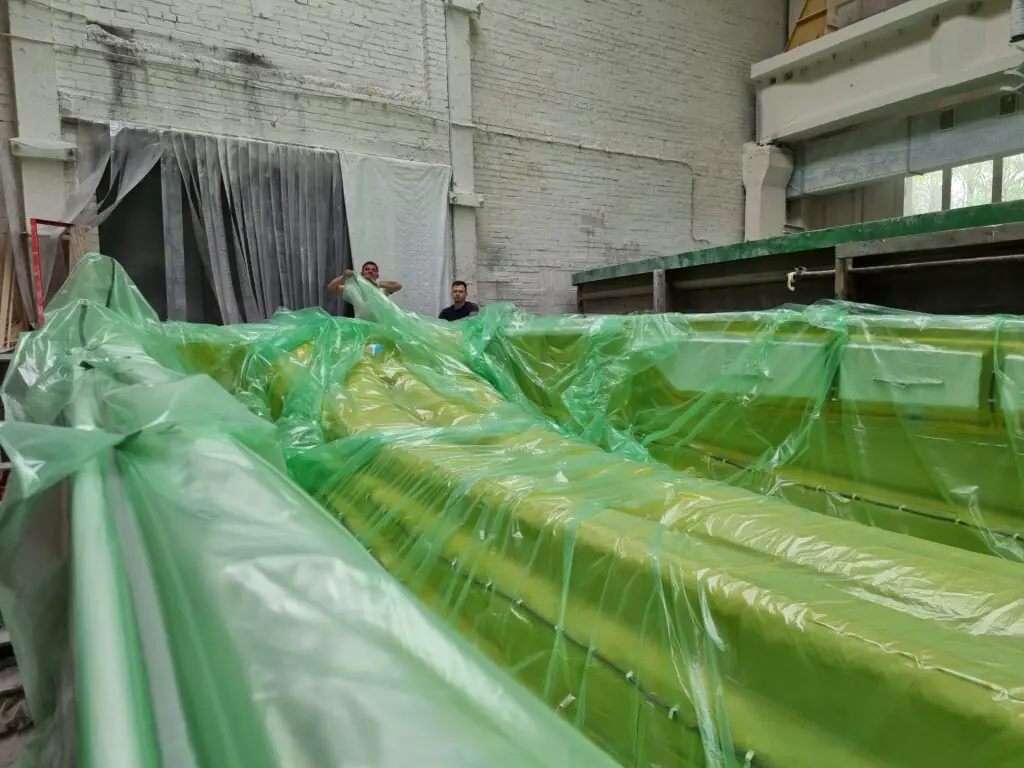
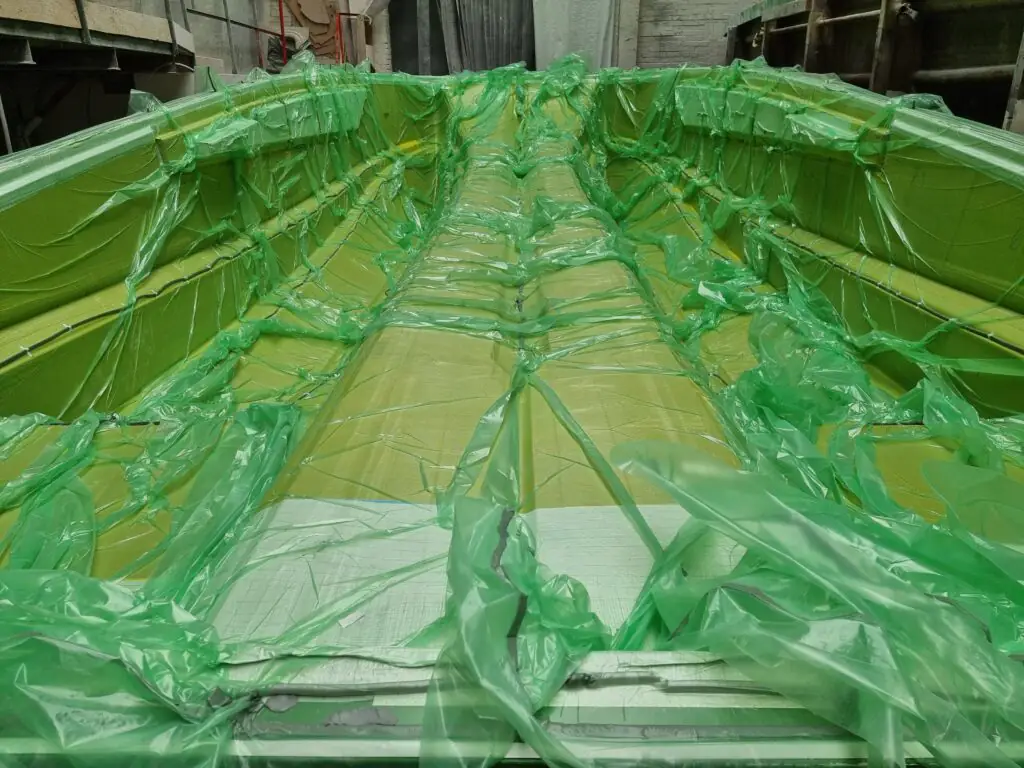
20 resin tubes were used to supply the resin during infusion, and the process was closely supervised and monitored to check the resin flow ran as predicted as it was pulled through by the vacuum.
The final process was nearly odourless, and used exactly the amount of resin predicted. .
Finally, with the material fully soaked the process was completed. This was a successful resin infusion of a power catamaran.
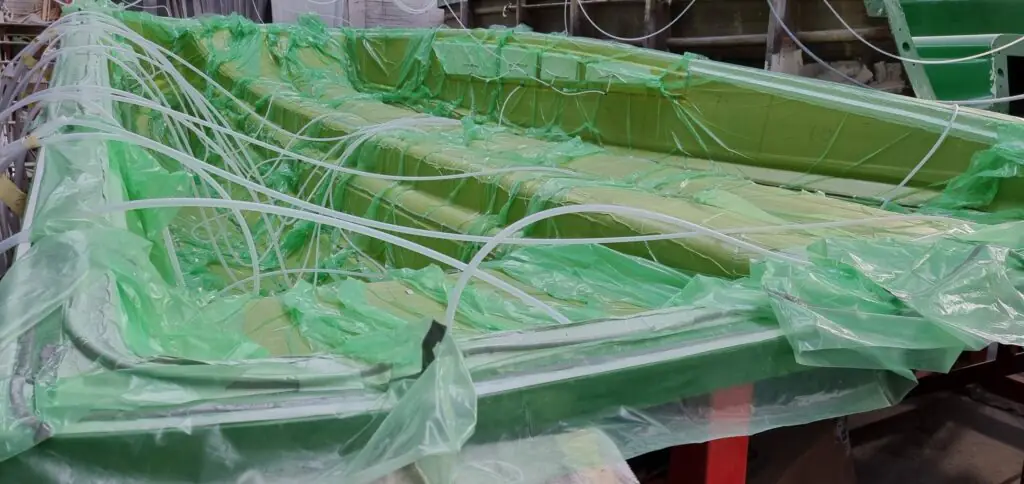